How to Use the Inventory Formula for Effective Stock Management
.webp)
Understanding the inventory formula is essential for businesses of all sizes, but it's especially crucial for small businesses where resources are limited, and efficiency is key. The inventory formula provides a reliable framework for managing stock, optimizing purchasing decisions, and maintaining a healthy balance between demand and supply.
What is the Basic Inventory Formula for Small Businesses?
For small business owners, getting a grip on inventory management can be the linchpin of success. The basic inventory formula, which calculates the Cost of Goods Sold (COGS), is straightforward: Beginning Inventory + Net Purchases - Ending Inventory = COGS. It's a simple yet powerful tool to understand what you have, what you need, and what you've sold.
Calculating Inventory Turnover with Precision
Calculating inventory turnover is critical for understanding how efficiently a business is managing its inventory and how often the inventory is sold and replaced over a specific period. This calculation not only helps businesses monitor stock levels but also guides strategic decisions regarding purchasing and sales practices. Here’s a detailed breakdown of how to calculate and utilize the inventory turnover ratio:
Steps to Calculate Inventory Turnover:
Determine COGS: Start by calculating the Cost of Goods Sold during the period you are analyzing.
Calculate Average Inventory: Average inventory can be estimated by adding the beginning inventory and ending inventory for the period, then dividing by two.
Use the Formula: Divide the COGS by the average inventory to find the inventory turnover ratio.
Analyzing Inventory Turnover Results:
Benchmarking: Compare your turnover ratio with industry standards to assess if your stock is moving faster or slower than the norm.
Trend Analysis: Look at changes in your inventory turnover over multiple periods to identify trends, improvements, or declines in inventory management.
Strategic Implications of Inventory Turnover:
Purchasing Decisions: A high turnover rate might suggest understocking and lost sales opportunities, prompting a review of purchasing policies.
Pricing Strategies: If turnover is low, consider promotional strategies or discounts to increase sales velocity.
Stock Optimization: Adjust stock levels based on turnover insights to balance having enough stock to meet customer demands without overstocking.
The Ending Inventory Formula Decoded
For retail stores, accurate calculation of ending inventory is crucial as it not only affects financial statements but also plays a pivotal role in strategic planning and tax reporting. The basic formula for calculating ending inventory is: Beginning Inventory + Net Purchases – COGS = Ending Inventory. Here are detailed steps and considerations to help retail stores effectively manage and calculate ending inventory:
Components of Ending Inventory Calculation:
- Record All Purchases: Account for all items bought during the period, which have been added to the inventory.
- Adjust for Returns: Deduct returned items to accurately reflect the inventory available for sale.
- Apply Discounts and Markdowns: Factor in any price reductions to determine the true retail value of the inventory.
Calculating Ending Inventory Using the Formula:
- Starting with the Beginning Inventory: This is the value of inventory carried over from the end of the last accounting period.
- Adding Net Purchases: Include the cost of all purchases made during the period, adjusting for returns and discounts.
- Subtracting COGS: Deduct the total cost of goods that have been sold during the period to arrive at the ending inventory value.
Valuation Methods:
- FIFO (First-In, First-Out): This method assumes the items purchased first are sold first, which is useful during periods of price increases.
- LIFO (Last-In, First-Out): Assumes the most recent purchases are sold first, beneficial in times of decreasing prices.
- Weighted Average Cost (WAC): Calculates the average cost of all items available during the period and is ideal when dealing with homogeneous products.
Utilizing Technology for Accuracy:
- Perpetual Inventory Systems: These systems continuously update inventory records for each purchase and sale, providing real-time inventory data which helps in precise calculation of ending inventory.
- Integration with Sales and Purchasing Data: Advanced inventory management solutions integrate seamlessly with sales and purchasing modules to automatically reflect changes in inventory levels, ensuring accurate ending inventory calculations.
Trimming Excess Stock with the Inventory Formula
An excess of stock can strain storage and dent your cash flow. The inventory formula is a fantastic diagnostic tool to identify overstock and understock situations, allowing you to adjust orders to match your sales trends.
Just-In-Time Systems and the Inventory Formula
Just-in-time inventory systems are all about efficiency, and the inventory formula fits right in. By tracking your COGS and ending inventory closely, you can order stock just as it's needed, reducing waste and storage costs.
The Central Role of the Inventory Formula in Supply Chain Management
In supply chain management, the inventory formula serves as the backbone for decision-making. It significantly influences purchasing, warehousing, and distribution, ensuring that each link in the chain is strong and responsive to market demands. Below are detailed bullet points that expand on how the inventory formula impacts various aspects of supply chain management:
Influencing Purchasing Decisions:
- Forecasting Demand: Utilizing historical inventory data to predict future product demands and adjust purchasing accordingly.
- Supplier Management: Deciding when and how much to order based on the inventory levels to maintain optimal stock without overstocking.
- Budget Optimization: Ensuring that purchasing decisions align with the financial constraints and goals of the business.
Enhancing Warehousing Efficiency:
- Layout Optimization: Arranging inventory to minimize retrieval time and maximize space utilization based on turnover rates and product categories.
- Safety Stock Levels: Calculating the right amount of safety stock to hold as a buffer against demand fluctuations and supply delays.
- Stock Accessibility: Organizing stock in a manner that aligns with the frequency and patterns of order fulfillment.
Streamlining Distribution Processes:
- Route Optimization: Using inventory levels and locations to determine optimal delivery routes and schedules.
- Customer Satisfaction: Ensuring product availability to meet customer demands promptly, enhancing reliability and trust.
- Cost Reduction: Minimizing transportation and handling costs by improving inventory accuracy and location strategies.
Adapting the Inventory Formula for Perishable Goods
When it comes to perishable goods, the inventory formula requires a slight tweak. It must accommodate faster turnover rates and the inevitable waste due to spoilage, making accurate inventory counts and timely ordering even more critical.
Avoiding Common Pitfalls in Inventory Formula Application
Accuracy is key in applying the inventory formula. Missteps in inventory management, such as miscounting inventory, not updating records, or overlooking returned goods, can lead to significant problems that may disrupt business operations. To help ensure that your inventory management remains precise and effective, consider the following detailed bullet points outlining strategies to avoid common pitfalls:
Preventing Miscounts:
- Regular Audits: Conduct physical counts of inventory regularly to ensure that the numbers match up with what's on the books.
- Use of Technology: Implement barcode scanners and inventory management software to reduce human error in counting and tracking stock.
- Training Staff: Ensure that all employees involved in inventory management are properly trained on correct counting procedures and the importance of accuracy.
Updating Inventory Records Promptly:
- Automated Systems: Utilize automated systems that update inventory levels in real-time as sales and restocking occur.
- Clear Protocols: Establish clear protocols for updating inventory records, including who is responsible and when updates should be made.
- Regular Reconciliation: Schedule regular reconciliation of physical stock to the inventory records to catch and correct any discrepancies early.
Accounting for Returned Goods:
- Dedicated Process: Have a dedicated process in place for handling returns that includes inspection, restocking, and record updates.
- Real-Time Adjustments: Ensure that inventory records are adjusted in real-time when returns are processed to maintain accurate data.
- Analysis of Returns: Regularly analyze the reasons behind returns to identify potential issues with products or sales processes that may be affecting inventory accuracy.
Inventory Formula for E-Commerce Platforms
E-commerce platforms must be agile, and using the inventory formula helps maintain this agility. It enables precise tracking of stock levels in real-time, which is essential for online businesses that deal with a global customer base and fast shipping expectations. To effectively implement and utilize the inventory formula in e-commerce, consider the following detailed strategies:
Real-Time Inventory Updates:
- Integration with Sales Channels: Ensure that inventory systems are integrated with all sales channels to automatically update stock levels as sales occur.
- Use of Cloud-Based Software: Adopt cloud-based inventory management systems that allow for real-time tracking and accessibility from any location.
- Notifications for Low Stock: Set up automated notifications to alert when stock levels are low, enabling timely replenishment and preventing stockouts.
Managing Global Inventory:
- Localized Warehousing: Use localized warehousing solutions to reduce shipping times and costs, adjusting inventory levels based on regional sales trends.
- Diverse Supplier Networks: Develop relationships with multiple suppliers to diversify sources of goods, reducing the risk of inventory shortages.
- Customs and Import Considerations: Keep track of inventory needs considering customs delays and import regulations that could affect stock availability.
Optimizing Fulfillment and Shipping:
- Automated Order Processing: Implement automated systems to process orders more quickly and accurately, minimizing handling time and speeding up delivery.
- Strategic Shipping Partnerships: Partner with reliable shipping companies that can provide fast and efficient service to meet customer expectations.
- Analysis of Shipping Data: Regularly analyze shipping and fulfillment data to identify trends and potential areas for optimization.
Conclusion
Understanding the inventory formula is not just about maintaining numbers but is a strategic tool that significantly enhances the operational efficiency of a business. By diligently applying this formula, businesses can achieve a delicate balance between overstocking and stockouts, ensure accurate financial reporting, and optimize their purchasing strategies. Moreover, it serves as a critical element in managing cash flows and improving customer satisfaction through better service levels. Thus, the effective use of the inventory formula can lead to substantial improvements in a company's financial health and competitive positioning.
To further enhance your inventory management capabilities, consider using Atomix App. With this innovative app, clients can easily monitor their inventory levels, streamline their operations, and make more informed decisions. Explore how Atomix Logistics App can transform your inventory management by reaching out to us today!
FAQ
What is the inventory formula?
The inventory formula is a basic calculation used to determine the Cost of Goods Sold (COGS) in a business. It is expressed as:
Beginning Inventory + Purchases - Ending Inventory = COGS
This formula helps businesses track how much inventory is used in a given period, aiding in financial and stock management.
How do you calculate the beginning inventory?
Beginning inventory refers to the value of stock held by a business at the start of an accounting period. It is typically the same as the ending inventory from the previous period. If not recorded, it can be calculated by adding the previous period’s COGS to its ending inventory and then subtracting the purchases made during that period.
What is meant by ‘Ending Inventory’?
Ending inventory is the value of goods available for sale at the end of an accounting period. It is calculated by physically counting the stock and valuing it at either cost or market price. Accurate ending inventory calculation is crucial for determining the next period’s beginning inventory and the current period’s COGS.
How does inventory turnover impact business operations?
Inventory turnover is a measure of how quickly a business sells through its stock of goods. A higher turnover rate can indicate strong sales or ineffective buying (understocking), whereas a lower turnover might indicate weak sales or excess inventory. Managing turnover helps businesses optimize their stock levels to meet customer demand without overcapitalizing on inventory.
What are common mistakes to avoid when using the inventory formula?
When using the inventory formula, common mistakes include:
- Miscounting Inventory: Errors in counting can lead to incorrect stock data, affecting all subsequent calculations.
- Not Updating Records Timely: Delayed record updates can cause discrepancies between physical stock and recorded figures, leading to misinformed decisions.
- Ignoring Returned Goods: Failing to account for returns in inventory records can inflate sales figures and distort the inventory count.
Talk with a team member and get $1,000 of order fulfillment credit*
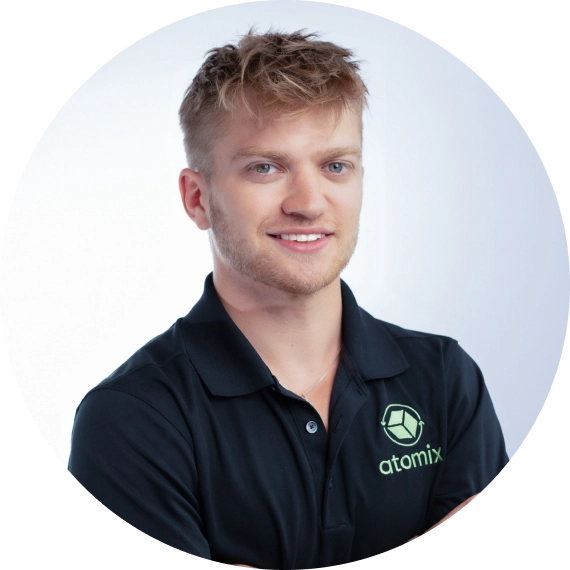
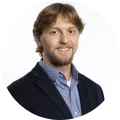
*$1,000 of credit is applied to customers account after Atomix fulfills their 500th order