Ensuring Product Quality Control During High-Volume Periods
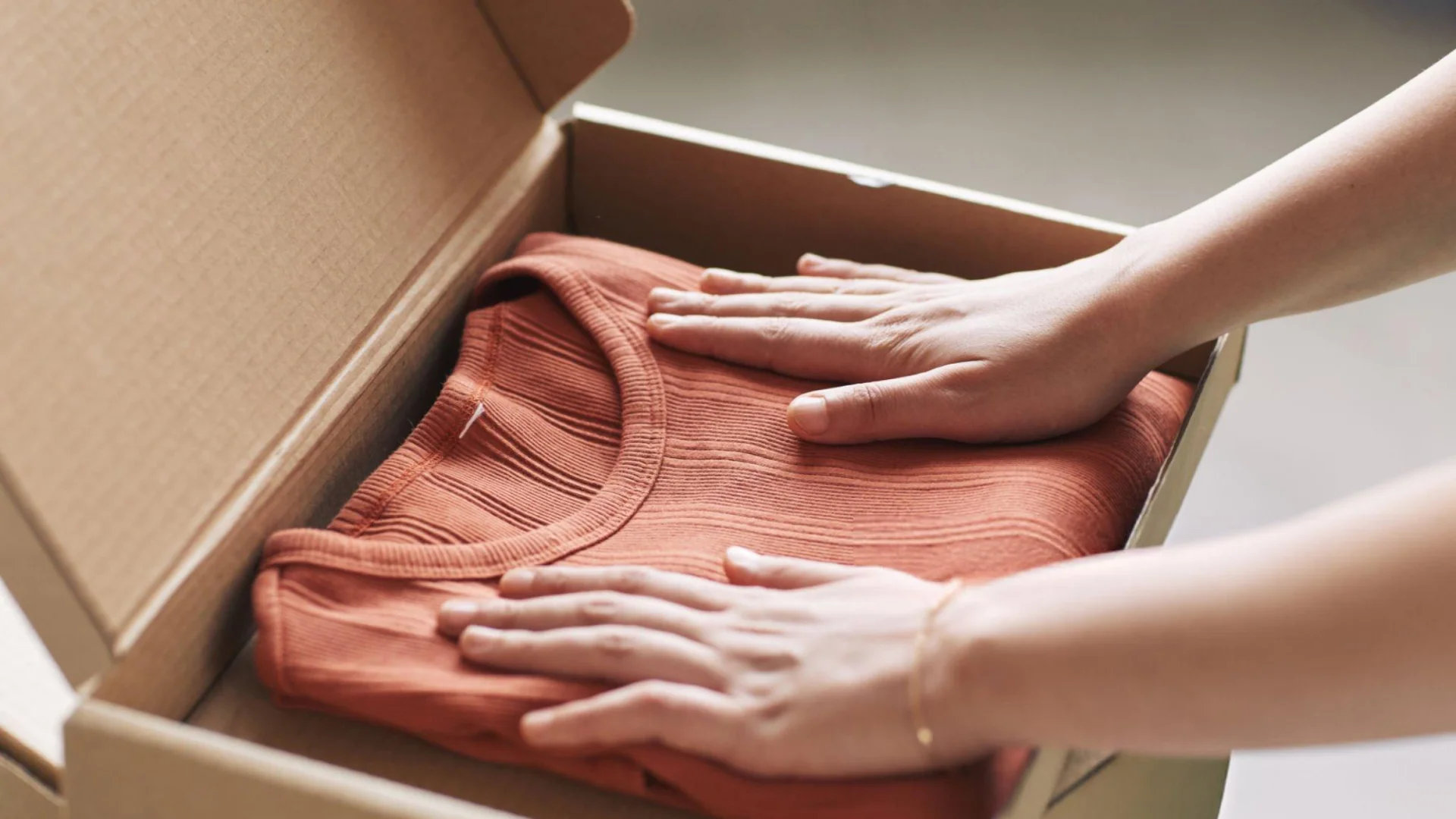
In today's fast-paced manufacturing environment, maintaining product quality control is crucial, especially during high-volume periods. When production lines are running at full speed, there’s an increased risk of defects, inefficiencies, and compliance issues. However, with the right strategies and processes in place, businesses can ensure that their products meet the highest manufacturing standards without compromising efficiency.
This article explores the best practices for ensuring quality control during high-volume production, offering insights into how manufacturers can optimize processes, minimize defects, and meet customer expectations while maintaining high standards.
The Importance of Product Quality Control in High-Volume Production
High-volume production periods, such as during seasonal demand spikes or large orders, place immense pressure on manufacturing systems. However, quality control must remain a top priority to prevent the costly consequences of defects, rework, and customer dissatisfaction.
Why Focus on Quality Control?
- Customer Satisfaction: The quality of your product directly impacts your customers' satisfaction. Poor quality leads to complaints, returns, and a damaged brand reputation.
- Cost Control: Defects in production can result in expensive rework, waste, or product recalls. Maintaining high-quality standards reduces these risks and helps keep production costs in check.
- Compliance Standards: Adhering to industry regulations and safety standards is critical. Failing to meet compliance standards can result in fines, penalties, or even the loss of business licenses.
Ensuring quality assurance and controlling defect rates during high-volume production requires a combination of skilled labor, technology, and efficient processes.
Strategies for Maintaining Product Quality Control
1. Optimize Your Standard Operating Procedures (SOPs)
The foundation of quality control during any production period starts with well-defined standard operating procedures (SOPs). These are detailed instructions that guide workers through every step of the production process to ensure consistency and efficiency. By standardizing operations, companies can prevent human errors and increase overall production efficiency.
- Document SOPs Clearly: Make sure that all processes, from raw material handling to final product inspection, are thoroughly documented and easily accessible to workers.
- Update Regularly: As your production techniques evolve, so should your SOPs. Keep them up-to-date with the latest technological solutions and industry best practices.
2. Embrace Real-Time Monitoring and Automation
Incorporating real-time monitoring systems and automation in quality control helps manufacturers identify potential issues as they occur, rather than after the fact. Automated inspection systems, such as cameras or sensors, can detect defects in real-time, allowing for immediate corrective actions and reducing the number of defective products that reach the market.
- Use Data-Driven Decisions: Leverage data collected through monitoring systems to make informed decisions about quality improvements and process optimization.
- Implement Automation: Automation can take over repetitive tasks and improve precision in areas where human error is likely, such as batch testing or material inspection.
3. Perform Root Cause Analysis for Defect Prevention
When defects do occur, it’s important to investigate why they happened through root cause analysis. This process allows manufacturers to pinpoint the underlying issue and implement corrective actions to prevent it from recurring.
- Defect Prevention: Analyzing defects helps identify process weaknesses, faulty materials, or insufficient training, allowing for improvements that reduce future issues.
- Corrective Actions: Implement a structured system for addressing defects as they arise, ensuring the root cause is addressed and future defects are prevented.
4. Implement Continuous Improvement Practices
A culture of continuous improvement is essential for maintaining high-quality standards, especially during high-volume production. This mindset encourages constant evaluation and improvement of processes to ensure product consistency and efficiency.
- Use Feedback Loops: Establish feedback loops between production teams, quality control, and management. Regularly review performance and identify areas for improvement.
- Apply Lean Manufacturing Principles: Lean manufacturing focuses on minimizing waste and optimizing production processes. Applying these principles helps improve production efficiency and maintain quality during high-volume periods.
5. Utilize KPIs and Quality Metrics
To effectively manage and track quality, manufacturers should establish clear Key Performance Indicators (KPIs) and quality metrics. These metrics provide a tangible way to measure performance, identify trends, and spot areas for improvement.
- KPIs in Quality Control: Track metrics such as defect rates, throughput, and production scheduling adherence to ensure that quality is maintained without disrupting output.
- Performance Metrics: Set benchmarks for performance, such as production speed, defect rates, and compliance, to continuously measure how well your team is maintaining standards.
6. Invest in Employee Training and Team Collaboration
During high-volume production, your workforce plays a critical role in maintaining quality assurance. Well-trained employees are more likely to follow SOPs correctly, identify issues early, and contribute to continuous improvement efforts.
- Employee Training: Regularly train employees on the latest inspection techniques, equipment use, and quality standards. Ensure that new hires receive thorough training before participating in high-volume production runs.
- Foster Team Collaboration: Encourage collaboration between production, quality control, and management teams. Open communication and cross-functional teamwork help identify problems faster and improve problem-solving efficiency.
Advanced Quality Control Techniques for High-Volume Production
1. End-of-Line Testing and Quality Audits
End-of-line testing ensures that products meet all quality and compliance standards before leaving the production facility. This step is especially crucial during high-volume periods to catch any defects that earlier processes may have missed.
- End-of-Line Testing: Test finished products for functionality, safety, and durability to ensure they meet customer and regulatory expectations.
- Quality Audits: Conduct regular audits of both your processes and products. These audits help ensure that your manufacturing operations are in line with industry compliance standards and internal quality expectations.
2. Real-Time Data Analysis for Immediate Corrections
Data from real-time monitoring systems can be analyzed on the fly to enable immediate corrections during production. This data-driven decision-making helps to spot defects or inefficiencies as they happen, reducing downtime and ensuring smoother operations.
- Real-Time Monitoring Systems: Utilize technologies that provide immediate feedback on product quality, machine performance, and process adherence.
- Corrective Actions in Real Time: By implementing real-time data analysis, issues like material defects, machine malfunctions, or employee errors can be corrected before they affect the entire production batch.
3. Material Inspection and Batch Testing
Consistent material inspection and batch testing are essential to ensuring that raw materials meet the required quality standards before they enter the production process. This proactive approach helps prevent defects caused by subpar materials and ensures product consistency.
- Material Inspection: Inspect incoming materials to verify they meet specifications and are free from defects.
- Batch Testing: Test random samples from each production batch to ensure consistency and detect potential issues before products are shipped to customers.
Risk Management and Compliance in Quality Control
High-volume production increases the risk of non-compliance and safety violations. Effective risk management ensures that your production process meets both industry regulations and internal safety standards.
1. Risk Management Strategies
- Identify Risks: Regularly assess your production process for potential risks, such as bottlenecks, equipment failure, or supply chain issues.
- Mitigate Risks: Implement measures such as preventative maintenance, supplier quality checks, and process improvements to mitigate identified risks.
2. Compliance with Industry Regulations and Safety Standards
Every industry has its own set of regulations that manufacturers must adhere to. Ensuring compliance not only avoids costly fines but also ensures the safety and quality of your product.
- Regulatory Compliance: Stay informed about changes to industry regulations and ensure your quality control processes meet these evolving standards.
- Safety Standards: Adhering to safety standards is essential, especially during high-volume periods when there is a higher risk of accidents or product failures.
Conclusion
Maintaining product quality control during high-volume periods is a challenging but essential task. By implementing robust processes, leveraging automation in quality control, and fostering a culture of continuous improvement, manufacturers can reduce defect rates, ensure product consistency, and meet customer demands efficiently.
From real-time monitoring to root cause analysis, the strategies outlined in this guide provide a roadmap for optimizing your production process without sacrificing quality. By focusing on key areas such as employee training, standard operating procedures, and risk management, businesses can thrive even during the most demanding production periods.
Maintaining high standards of quality in manufacturing isn't just about meeting compliance standards; it’s about delivering products that meet customer expectations, reduce waste, and build long-term success.
FAQ: Ensuring Product Quality Control During High-Volume Periods
What are the best practices for maintaining product quality control during high-volume production?
To maintain product quality during high-volume production, it's essential to implement clear standard operating procedures (SOPs), leverage automation in quality control, conduct regular batch testing, and use real-time monitoring to detect issues early. Training employees and fostering team collaboration also play critical roles in ensuring consistency and reducing defects.
How does automation improve quality control in manufacturing?
Automation in quality control helps by reducing human error, increasing precision, and enabling real-time defect detection. Automated systems can conduct consistent material inspections, perform end-of-line testing, and track key performance metrics to ensure product consistency and improve overall production efficiency during high-volume periods.
What are the key metrics to track for quality control in manufacturing?
Key metrics for quality assurance include defect rates, production efficiency, adherence to compliance standards, and the performance of real-time monitoring systems. Additionally, KPIs (Key Performance Indicators) like production throughput, batch testing results, and waste reduction are crucial for tracking the effectiveness of quality control processes.
How do you prevent defects in high-volume manufacturing?
Preventing defects in high-volume production involves conducting thorough root cause analysis when issues arise, regularly updating standard operating procedures, and using data-driven decisions to implement process optimization. Ongoing employee training, risk management strategies, and leveraging automation in quality control are also effective ways to prevent defects.
Why is real-time monitoring important for product quality control?
Real-time monitoring allows manufacturers to detect issues immediately as they occur, rather than after production. This enables quick corrective actions, minimizes downtime, and helps maintain product consistency during high-volume periods. It also supports data-driven decisions to continuously improve the production process and reduce defect rates.
Talk with a team member and get $1,000 of order fulfillment credit*
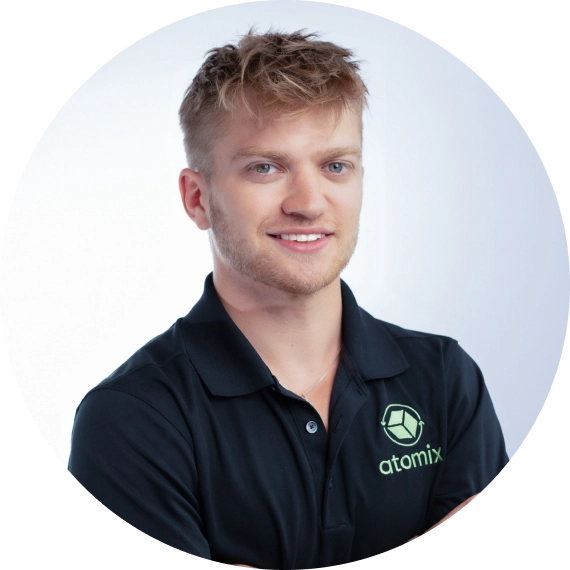
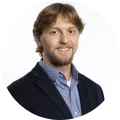
*$1,000 of credit is applied to customers account after Atomix fulfills their 500th order