What Is Stock Management and How Can It Improve Your Business Operations?
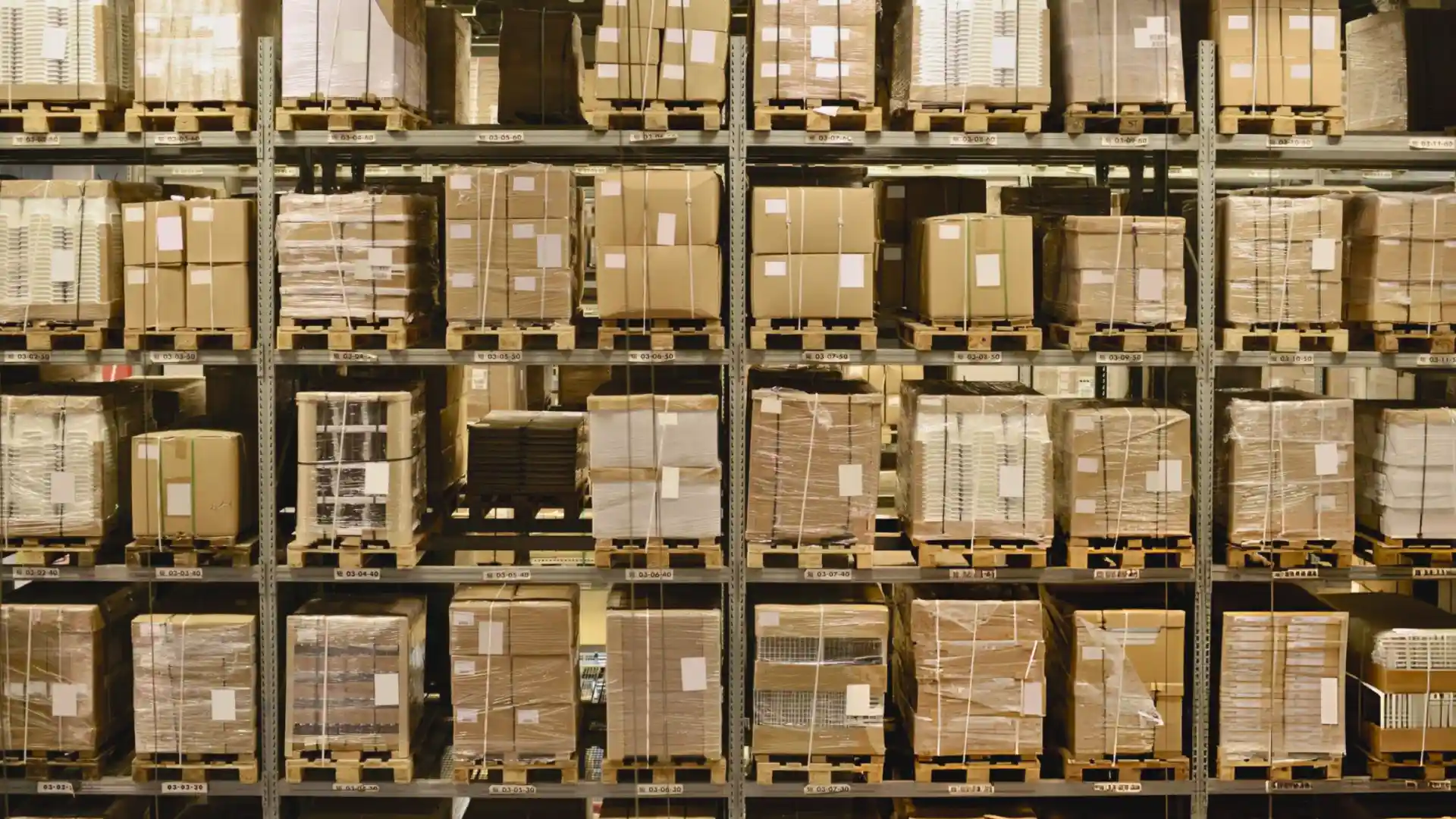
Effective stock management is at the heart of any successful business, whether you're an e-commerce giant like Amazon or a small retail shop on Etsy. Properly managing your stock means avoiding overstocking, stockouts, and understanding how to calculate key stock-related metrics. In this blog post, we’ll dive deep into what stock means, different types of stock, key stock-related formulas, and how to optimize your stock for the best outcomes. We’ll also highlight important concepts like dead stock, safety stock, stock turnover, and more.
What Does Stock Mean?
At its most basic level, stock refers to the goods and materials that a business holds for the purpose of resale or manufacturing. Stock can include everything from raw materials to finished products. For retailers, the term "in stock" means that the item is available for sale, while "out of stock" indicates that the item is currently unavailable.
However, managing stock is much more complex than just knowing what's available. It requires a deep understanding of supply chains, customer demand, and the nuances of different types of stock, such as bonded stock, dead stock, and seasonal stock.
Defining Key Stock Terms
1. Backstock Meaning
Backstock refers to inventory that is not on the sales floor but is stored in a warehouse or stockroom. It’s essentially a backup supply to ensure that customers can be serviced quickly when the on-hand inventory runs low.
2. Dead Stock
Dead stock is inventory that hasn't sold and is unlikely to sell in the future. Dead stock could be due to obsolete items, over-ordering, or products that were seasonal in nature. Dead stock is not only a financial burden but also a logistical one. Some dead stock stores try to sell off unsold inventory at discounted prices to clear it out.
3. Stock Turnover
Stock turnover, also known as inventory turnover, refers to the rate at which inventory is sold and replaced over a given period. The formula for calculating stock turnover ratio is essential for understanding how efficiently a business is managing its stock. We'll cover this formula in greater detail below.
4. Safety Stock
Safety stock is extra inventory kept on hand to reduce the risk of stockouts. The safety stock calculation formula is used to ensure that a business maintains an adequate buffer to meet customer demand, even if suppliers are delayed or demand unexpectedly increases.
Calculating Stock: The Equation for Safety Stock
To maintain an optimal inventory, calculating safety stock is a necessity. The safety stock equation helps determine how much extra stock you need to hold to account for variability in demand and supply. Here’s the formula for safety stock:
Safety Stock = (Max Daily Usage × Max Lead Time) - (Average Daily Usage × Average Lead Time)
This safety stock formula helps businesses maintain enough inventory to prevent stockouts during unforeseen circumstances. Companies using advanced warehouse stock management systems can automate this process to maintain accurate inventory records.
Common Stock Issues and How to Solve Them
Many businesses face challenges when it comes to managing stock. Here are some of the most common stock-related issues and how you can address them.
1. Overstocking
Overstocking occurs when a business holds more inventory than it needs, which ties up capital and increases storage costs. Overstocking is often caused by inaccurate demand forecasting or poor stock management practices.
Solution: Use advanced forecasting tools and regularly review inventory levels to avoid overstocking. Overstocked items can be sold through discount outlets or overstock warehouses to recoup some costs.
2. Stockouts
A stockout occurs when a business runs out of inventory for an item that is in demand. Stockouts can result in lost sales and frustrated customers. The key to preventing stockouts is maintaining the right level of safety stock and using accurate demand forecasts.
3. Dead Stock
As mentioned earlier, dead stock refers to items that have been in inventory for too long without selling. Holding onto dead stock can drain your finances and take up valuable storage space.
Solution: Regularly review your inventory to identify dead stock early. You can either discount these items to sell them quickly or bundle them with more popular products to move them out of your inventory.
Best Practices for Effective Stock Management
Stock management can make or break a business, which is why it’s essential to implement best practices. Here are some tips to keep your inventory in check:
- Use a Stock Management Software: Implementing the best stock management software allows businesses to automate many inventory control processes, from tracking stock levels to generating purchase orders.
- Monitor Stock Turnover: Regularly calculating stock turnover ratio helps identify slow-moving items and ensure you’re not tying up capital in unsellable goods.
- Optimize Safety Stock: By calculating safety stock based on demand forecasts and lead times, you can avoid both stockouts and overstock situations.
- Implement FIFO: For industries like food and pharmaceuticals, using the FIFO method to restock inventory is essential for preventing waste and maintaining quality control.
- Plan for Seasonal Demand: Effectively managing seasonal stock by forecasting demand spikes and slow periods can prevent excess inventory and missed opportunities.
- Regular Stock Audits: Periodic stock audits help ensure that the physical count matches your records, which is important for maintaining accuracy in your inventory.
- Collaborate with Experts: Working with logistics companies like Atomix Logistics can take the burden of stock management off your shoulders. With our experience and cutting-edge technology, we help businesses streamline their inventory processes, saving both time and money.
How to Restock Efficiently
Efficient restocking is vital for businesses that deal with high-volume or fast-moving inventory, such as grocery stores or e-commerce platforms.
FIFO Method for Restocking Food
The FIFO (First In, First Out) method is essential in industries like food service, where perishable goods need to be sold before they expire. This method ensures that older stock is sold first, reducing waste and ensuring product freshness.
How to Restock on Etsy
If you're an Etsy seller, maintaining a steady stock level is key to keeping customers happy. Etsy doesn't allow unlimited stock by default, so regularly updating your stock and tracking your inventory is essential. Tools like PS Portal Stock Tracker can help monitor stock levels, ensuring that you’re always ready to restock when needed.
Stock Management Software with Atomix Logistics
Effective stock management is the backbone of any successful business. With Atomix Logistics, businesses gain access to cutting-edge stock management software that simplifies the entire inventory process. Whether you're a small e-commerce store or a large corporation, managing your inventory efficiently can save you time, reduce costs, and boost overall profitability.
Atomix Logistics offers advanced stock management solutions tailored to your specific business needs, helping you streamline operations, prevent stockouts, and minimize overstocking. Here’s what you can expect from Atomix Logistics’ stock management software:
Benefits of Using Stock Management Software with Atomix Logistics
- Real-Time Inventory Tracking: Gain visibility into your stock levels at any time, ensuring you're never caught off guard by stockouts or overstocking.
- Warehouse Integration: Seamlessly connect your warehouse operations with the software for better coordination between stock movement and order fulfillment.
- Customizable Reporting: Generate detailed reports on stock turnover, dead stock, and safety stock levels, giving you the insights needed to make informed decisions.
- Multi-Channel Support: Manage stock across multiple sales channels, from online platforms like Amazon and Etsy to physical retail stores, all from a single dashboard.
Conclusion
Effective stock management is vital for keeping your business running smoothly. From understanding the basic definitions like backstock and safety stock to mastering complex formulas like the safety stock equation, there are many elements to juggle. However, by using the best stock management software, partnering with experts like Atomix Logistics, and implementing tried-and-true strategies like the FIFO method, you can ensure that your stock is always optimized to meet customer demand while keeping costs low.
Whether you're calculating your stock turnover ratio or figuring out how to avoid dead stock, managing your inventory efficiently is key to your business’s success.
Stock Management FAQ
What is stock turnover, and how can I calculate it?
Stock turnover, also known as inventory turnover, is the rate at which a business sells and replaces its inventory over a given period. To calculate the stock turnover ratio, use the formula:
Stock Turnover Ratio = Cost of Goods Sold (COGS) / Average Inventory
This calculation helps businesses understand how efficiently they are managing their stock, which is essential for maintaining optimal inventory levels.
What is dead stock, and how can I avoid it?
Dead stock refers to inventory that hasn't sold and is unlikely to sell due to obsolescence, over-ordering, or seasonality. Holding on to dead stock can lead to financial losses and take up valuable storage space. To avoid dead stock, regularly review your inventory, discount slow-moving items, or bundle them with popular products to clear them from your stock.
How do I calculate safety stock, and why is it important?
Safety stock is extra inventory kept on hand to prevent stockouts during unexpected demand surges or supply chain delays. To calculate safety stock, use this formula:
Safety Stock = (Max Daily Usage × Max Lead Time) - (Average Daily Usage × Average Lead Time)
By maintaining the right level of safety stock, businesses can avoid lost sales due to stockouts and maintain smooth operations even during supply chain disruptions.
What is backstock, and how does it affect my inventory?
Backstock refers to inventory stored in a warehouse or stockroom that is not immediately available for sale on the sales floor. It serves as a backup supply to meet customer demand when on-hand stock runs low. Properly managing backstock ensures you can quickly replenish shelves and avoid stockouts, helping maintain smooth sales flow.
Talk with a team member and get $1,000 of order fulfillment credit*
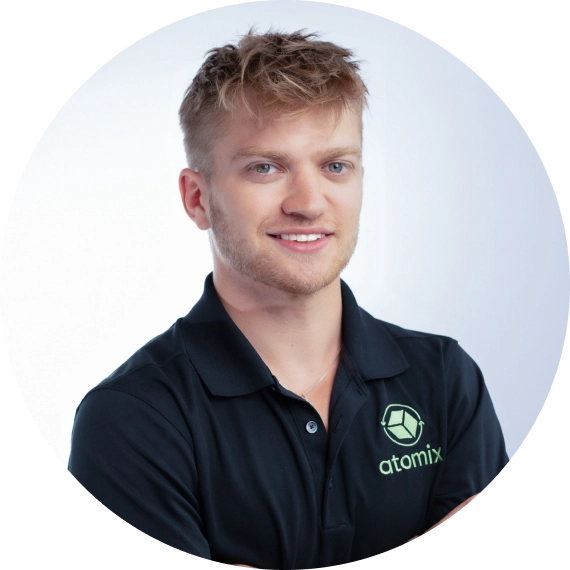
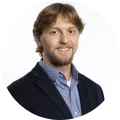
*$1,000 of credit is applied to customers account after Atomix fulfills their 500th order