How to Ensure Timely Deliveries During Peak Seasons
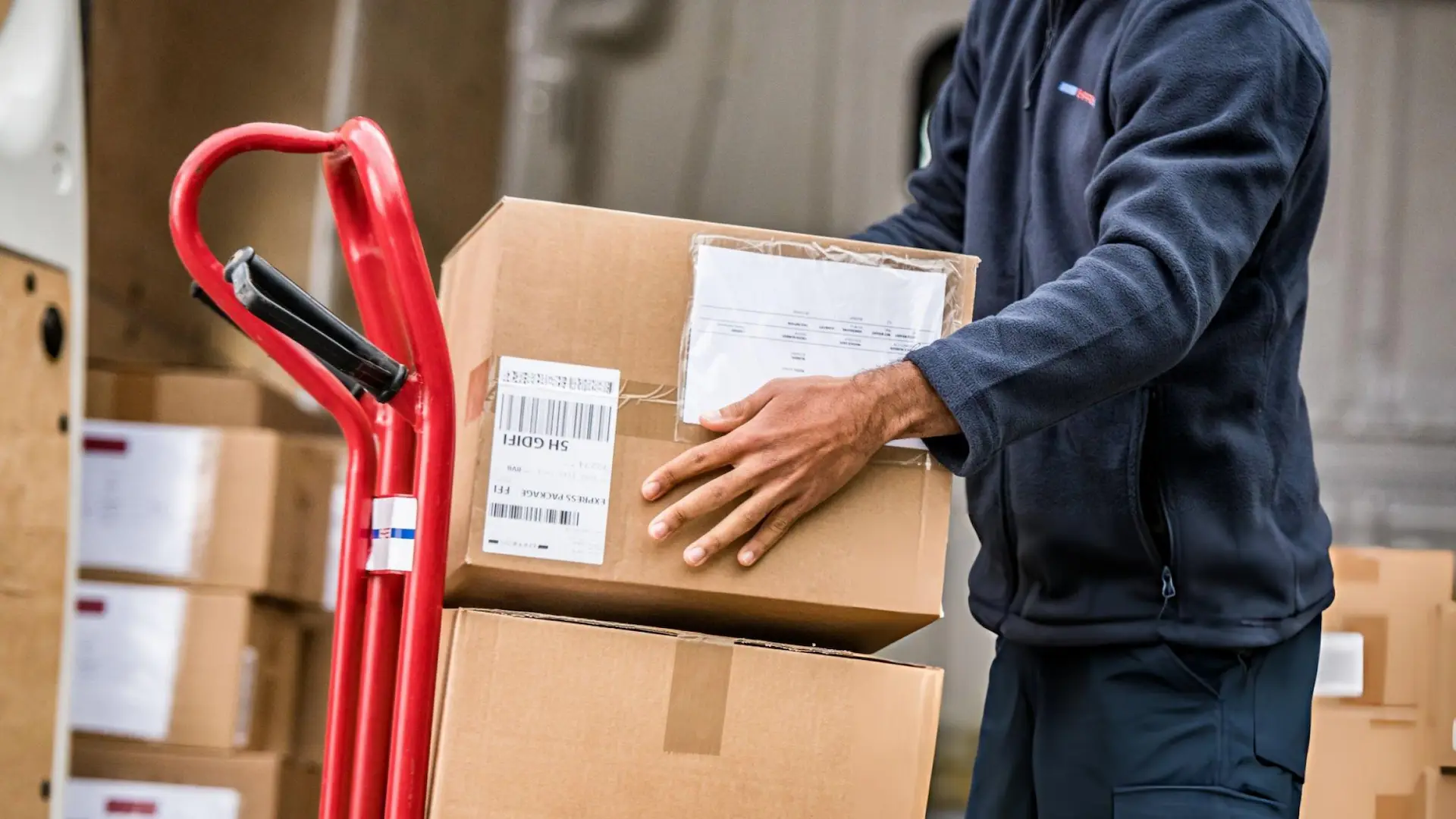
Meeting delivery deadlines during peak seasons can be a challenge, especially with surging order volumes, supply chain disruptions, and carrier capacity constraints. Businesses that implement effective peak season shipping strategies can keep customers satisfied and maintain operational efficiency.
From on-time delivery optimization to real-time order tracking systems, several tactics help businesses navigate holiday season logistics planning successfully. This guide outlines key strategies for managing peak-season shipments, reducing delivery delays, and maintaining smooth operations.
1. Plan Ahead with Seasonal Demand Forecasting
Accurate seasonal demand forecasting methods allow businesses to anticipate order surges, allocate resources effectively, and prevent stock shortages. Analyzing past sales data, market trends, and consumer behavior helps businesses prepare for increased demand.
Steps to Improve Demand Forecasting:
- Analyze historical data – Reviewing past holiday sales trends provides insights into expected volume.
- Monitor market trends – Understanding consumer preferences and economic conditions helps refine predictions.
- Use predictive analytics – Advanced algorithms identify patterns and forecast inventory needs.
- Communicate with suppliers – Aligning with vendors ensures stock availability and prevents delays.
2. Optimize Inventory Management During Busy Periods
Efficient inventory management during busy periods prevents stockouts and overstock situations. Proper planning allows businesses to meet customer demand without overloading storage capacity.
Best Practices for Inventory Optimization:
- Implement distributed inventory management – Storing products in multiple fulfillment centers shortens shipping distances.
- Leverage micro-fulfillment centers – Small-scale warehouses near urban areas speed up last-mile deliveries.
- Use real-time tracking – Monitoring stock levels helps prevent shortages and ensures accurate fulfillment.
- Integrate proprietary software – Custom inventory management tools streamline stock allocation and prevent errors.
3. Strengthen Warehouse Efficiency for Peak Season
A well-structured warehouse is essential for handling high order volumes. Peak season warehouse efficiency depends on streamlined workflows, automation, and optimized space utilization.
Ways to Improve Warehouse Operations:
- Optimize pick-and-pack processes – Arranging inventory strategically reduces time spent on order fulfillment.
- Implement automated fulfillment processes – Robotics and AI-driven sorting systems accelerate packing and shipping.
- Utilize cross-docking for faster deliveries – Directly transferring shipments from inbound to outbound trucks minimizes storage time.
- Increase temporary staffing – Hiring seasonal workers supports efficient handling of increased order volumes.
4. Implement Scalable Shipping Operations
Managing high-volume shipping periods requires flexibility in carrier selection and shipping methods. Multi-carrier shipping solutions reduce reliance on a single provider, ensuring seamless delivery options.
Key Shipping Strategies for Peak Season:
- Carrier capacity planning for holidays – Booking shipments in advance secures delivery slots with reliable carriers.
- Flexible delivery options for busy periods – Providing expedited, standard, and eco-friendly shipping choices improves customer satisfaction.
- Same-day delivery optimization – Using regional couriers and micro-fulfillment center implementation supports ultra-fast shipping.
- Weather-resistant shipping solutions – Protecting goods from extreme weather prevents damage and delays.
5. Optimize Last-Mile Delivery for Peak Seasons
Last-mile delivery optimization for peak seasons is crucial for maintaining customer satisfaction. The final leg of the shipping journey often faces the most delays due to traffic congestion, incorrect addresses, and carrier limitations.
Tactics to Improve Last-Mile Delivery:
- Use real-time order tracking systems – Providing customers with shipment updates improves transparency and trust.
- Leverage omnichannel fulfillment strategies – Offering in-store pickup, locker delivery, and local couriers reduces last-mile bottlenecks.
- Streamline returns management – Simplifying returns with prepaid labels and drop-off locations enhances customer experience.
- Utilize predictive analytics in peak season logistics – AI-driven route optimization minimizes transit time and fuel costs.
6. Strengthen Customer Communication During Peak Seasons
Clear customer communication during peak seasons helps set realistic expectations and reduces inquiries about order status. Transparency is key to maintaining trust and reducing frustration.
Effective Communication Strategies:
- Provide accurate delivery estimates – Displaying expected shipping times at checkout prevents misunderstandings.
- Use automated notifications – Sending SMS and email updates keeps customers informed about shipment progress.
- Offer proactive support – Addressing delays promptly and offering solutions minimizes complaints.
- Implement EDI connections – Automating order updates between retailers and logistics partners enhances accuracy.
7. Leverage Technology Solutions for Peak Season Shipping
Advanced technology solutions for peak season shipping streamline logistics operations and improve efficiency. From AI-powered demand forecasting to automated fulfillment platforms, digital tools play a significant role in optimizing deliveries.
Key Technologies for Peak Season Logistics:
- Fulfillment platform integration – Connecting sales channels with logistics systems improves order processing.
- Automated freight booking – Digital freight matching platforms expedite carrier selection.
- Custom 3PL solutions – Partnering with third-party logistics providers like Atomix Logistics enhances scalability.
- IoT-enabled real-time tracking – Smart sensors monitor shipments and prevent loss or theft.
8. Manage Shipping Deadlines and Reduce Holiday Delays
Shipping deadline management ensures customers receive orders on time despite peak-season demand. Businesses that set clear cutoffs for different shipping methods reduce last-minute rushes and missed deadlines.
Tips to Avoid Delivery Delays:
- Set order cutoff dates – Communicating last purchase dates for holiday arrivals helps customers plan ahead.
- Increase fulfillment speed – Expanding warehouse shifts and automation accelerates processing.
- Offer alternative delivery methods – Same-day, local pickup, and expedited shipping provide backup options.
- Monitor carrier performance – Tracking delivery success rates helps identify the most reliable shipping partners.
Conclusion
Timely deliveries during peak seasons require careful holiday season logistics planning, proactive inventory management during busy periods, and seamless last-mile delivery execution. By adopting efficient order fulfillment techniques, leveraging technology, and strengthening peak season warehouse efficiency, businesses can successfully navigate high-demand periods.
Atomix Logistics specializes in ecommerce fulfillment, subscription boxes, and custom packaging, ensuring smooth operations during peak shipping periods. With 3PL services, proprietary software, and temp controlled storage, businesses can optimize their logistics strategies for faster, more reliable deliveries. Get your fulfillment quote today!
Frequently Asked Questions (FAQs)
What are the best peak season shipping strategies to prevent delays?
To minimize delays during peak seasons, businesses should implement multi-carrier shipping solutions, use real-time order tracking systems, and optimize last-mile delivery. Additionally, seasonal demand forecasting methods help anticipate order surges, allowing companies to allocate inventory efficiently and avoid stockouts.
How can businesses improve on-time delivery optimization during the holidays?
Companies can enhance on-time delivery optimization by refining their warehouse efficiency, automating fulfillment with proprietary software, and strengthening carrier capacity planning for holidays. Using predictive analytics in peak season logistics also helps identify potential bottlenecks and optimize delivery routes.
What role does inventory management play during busy periods?
Inventory management during busy periods is critical for meeting customer demand without overstocking or running out of products. Businesses should adopt distributed inventory management, leverage micro-fulfillment centers, and integrate real-time tracking systems to ensure stock availability across multiple locations.
How can companies reduce delivery delays during holidays?
To reduce delivery delays during holidays, businesses should secure carrier contracts in advance, expand warehouse staff with peak season staffing strategies, and offer flexible delivery options for busy periods. Implementing weather-resistant shipping solutions also helps protect shipments from seasonal disruptions.
What technology solutions help optimize peak season shipping?
Advanced technology solutions for peak season shipping include automated fulfillment processes, real-time tracking systems, and AI-powered data-driven peak season planning. Partnering with 3PL services like Atomix Logistics, which provides custom 3PL solutions, freight booking, and EDI connections, can further streamline shipping operations.
Talk with a team member and get $1,000 of order fulfillment credit*
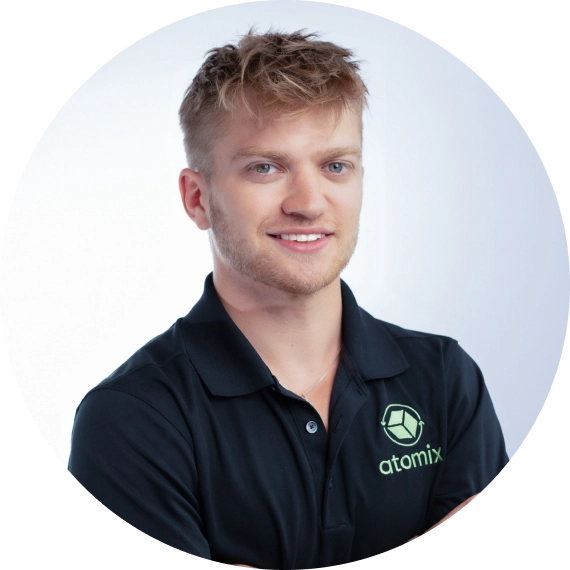
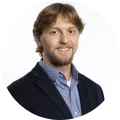
*$1,000 of credit is applied to customers account after Atomix fulfills their 500th order