What Do Fulfillment Centers Do? Everything You Need to Know
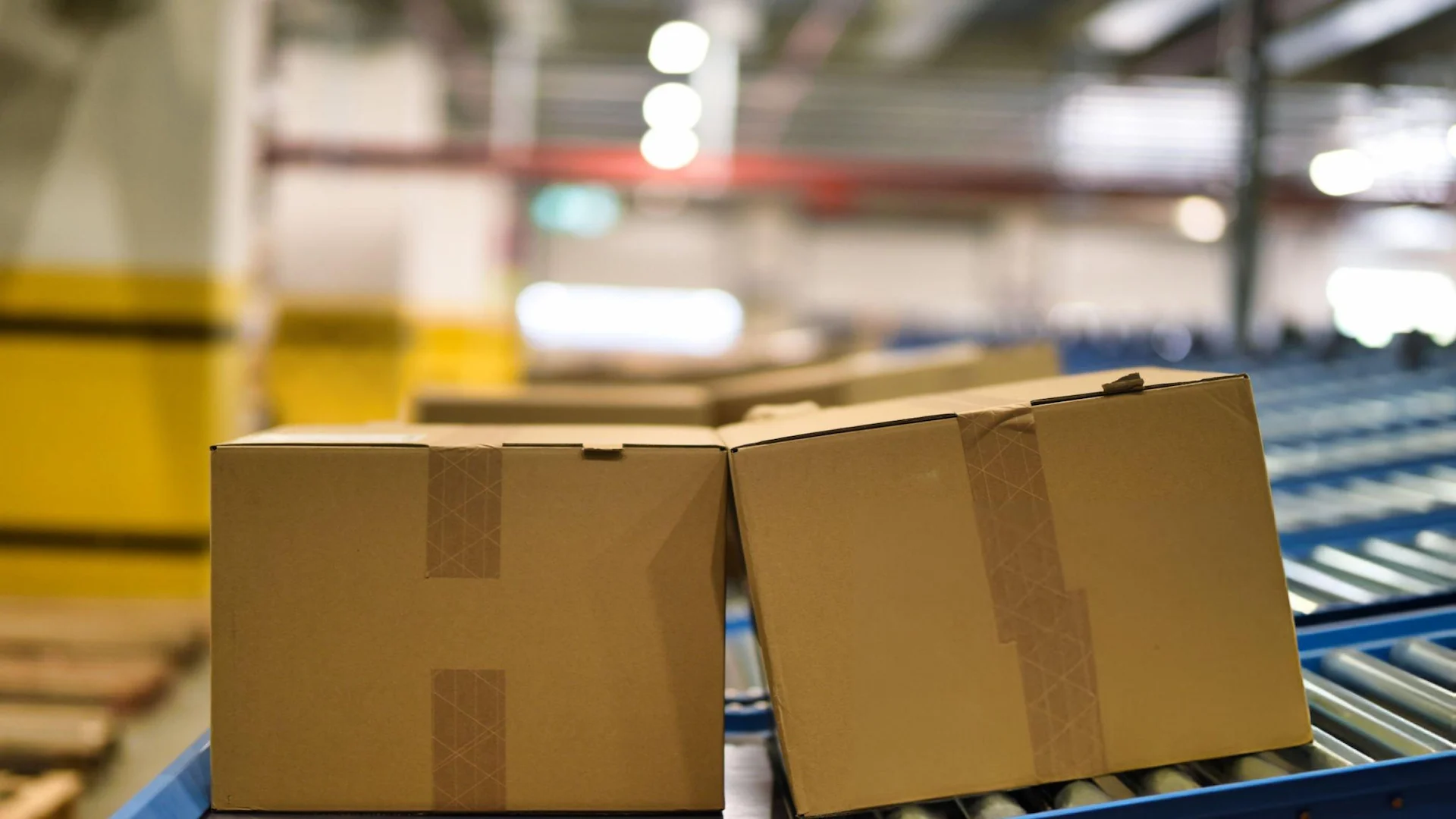
For ecommerce brands seeking to scale quickly, a reliable fulfillment strategy is non-negotiable. Fulfillment centers play a critical role in helping businesses meet customer expectations for fast, accurate deliveries. By handling complex logistics behind the scenes, they allow brands to focus on growth and innovation.
Partnering with a trusted provider like Atomix Logistics delivers the order fulfillment support ecommerce brands need to succeed in a competitive marketplace.
What Is a Fulfillment Center?
A fulfillment center is a specialized facility where ecommerce orders are processed from beginning to end. Products are received, stored, picked, packed, and shipped to customers with the goal of speed and efficiency. Fulfillment centers often integrate seamlessly with ecommerce platforms, providing real-time updates on inventory, order status, and shipping details.
Compared to a traditional warehouse for ecommerce brands, a fulfillment center prioritizes rapid inventory turnover. Warehouses typically focus on long-term storage, while fulfillment centers are designed for fast movement of goods to end customers.
The demand for ecommerce fulfillment centers has grown with the rise of online shopping, making it essential for brands to have logistics partners capable of supporting quick and accurate deliveries.
Core Functions of Fulfillment Centers
Understanding what fulfillment centers do starts with their primary services. Here are the key functions:
Receiving and Storing Inventory
- Receiving: Fulfillment centers accept inventory shipments, inspecting goods for damage and accuracy.
- Storing: Products are organized using shelving, bins, or pallet racks, optimizing space for efficient retrieval.
Efficient receiving and storing practices support faster order fulfillment and accurate inventory tracking, critical for ecommerce shipping success.
Inventory Management
- Real-Time Tracking: Modern fulfillment centers use technology for real-time inventory tracking, minimizing stock discrepancies.
- Stock Control: Automated systems prevent overstocking or stockouts, supporting better business planning.
Inventory management ensures brands maintain the right stock levels, reducing costs tied to excess inventory and lost sales from out-of-stocks.
Order Picking and Packing
- Picking: Staff locate products quickly using digital picking systems or robotics.
- Packing: Orders are securely packed with brand-specific materials when requested.
Effective picking and packing are vital parts of the order fulfillment process. Atomix Logistics customizes packing methods to support each brand’s image.
Shipping
- Carrier Management: Fulfillment centers negotiate with multiple carriers to provide fast, affordable shipping options.
- Shipping Options: Customers benefit from same-day, next-day, or standard shipping based on their selection.
3PL shipping solutions offered through fulfillment centers streamline carrier management and improve delivery performance.
Returns Processing
- Reverse Logistics: Items returned by customers are processed, inspected, and either restocked or appropriately disposed of.
Managing returns efficiently not only protects inventory value but strengthens brand reputation through excellent post-purchase experiences.
Customer Service Support
- Some fulfillment providers offer customer support for tracking orders, handling delays, and managing returns inquiries.
High-quality support throughout the fulfillment center operations enhances brand loyalty and boosts repeat business.
How Fulfillment Centers Work: Step-by-Step
The fulfillment center process follows a streamlined sequence:
- Inventory Arrival: Products are shipped to the fulfillment center from the supplier or manufacturer.
- Receiving and Inspection: Goods are checked for quality, quantities are verified, and items are logged into the system.
- Inventory Storage: Products are shelved in optimized zones for fast picking.
- Order Integration: Ecommerce platforms connect through APIs to the order fulfillment software.
- Picking and Packing: Orders are picked and packed as soon as they are received.
- Shipping Coordination: Labels are printed, carriers are selected, and packages are sent out.
- Order Tracking: Customers and brands can track deliveries through real-time systems.
- Returns Management: Any returns are processed quickly, updating inventory and issuing refunds as needed.
Atomix Logistics leverages automation, real-time dashboards, and predictive inventory management to maximize every stage of this process.
Fulfillment Centers vs Warehouses: Key Differences
Understanding the difference between a fulfillment center vs warehouse for ecommerce brands is important when selecting a logistics partner.
FeatureFulfillment CenterWarehouseMain PurposeFast order processingLong-term storageIntegrationEcommerce, 3PL systemsLimitedInventory TurnoverRapidSlowServicesPicking, packing, shipping, returnsStorage onlyTechnologyAdvanced real-time trackingBasic systems
Choosing a fulfillment center supports rapid scaling and superior customer satisfaction, two crucial factors for growing ecommerce brands.
Benefits for Brand Decision Makers
There are clear advantages to working with a fulfillment partner like Atomix Logistics. Key benefits include:
Scalability
Fulfillment centers adapt easily during peak seasons, product launches, and rapid growth phases. Brands can expand without needing to invest in warehouses, additional staff, or infrastructure.
Efficiency
Streamlined operations, powered by automated order fulfillment solutions, reduce shipping errors, improve order accuracy, and accelerate delivery times.
Customer Experience
Fast shipping, accurate deliveries, and reliable returns management elevate customer satisfaction. A great fulfillment experience drives positive reviews, loyalty, and referrals.
Cost Savings
Using a 3PL fulfillment partner reduces fixed costs such as warehouse leases, utilities, and payroll. Brands gain access to volume shipping discounts and operational expertise without managing logistics internally.
Business Focus
Outsourcing order fulfillment allows brands to redirect energy toward marketing, product innovation, and customer acquisition rather than logistics management.
Atomix Logistics specializes in tailoring fulfillment solutions that meet the needs of growing ecommerce brands, making operations smoother and more profitable.
Choosing the Right Fulfillment Center Provider
The success of your ecommerce fulfillment strategy relies on choosing the right partner. Key factors to consider:
- Technology Integration: The fulfillment provider should integrate seamlessly with your ecommerce platform and order fulfillment software.
- Real-Time Visibility: Look for real-time inventory tracking, order status updates, and automated reporting.
- Service Range: Picking, packing, shipping, returns processing, and customer support must be part of the core offering.
- Scalability: The provider should accommodate your brand’s current and future growth.
- Customer Support: Dedicated account managers and responsive support teams simplify issue resolution.
- Pricing Transparency: Fee structures should be easy to understand with no hidden costs.
Atomix Logistics offers customized 3PL fulfillment services built to support ecommerce brands from startup phase to enterprise level, backed by an experienced team and advanced technology.
Why Fulfillment Centers Are a Growth Engine for Brands
Partnering with a fulfillment center is more than an operational decision. It’s a growth strategy. By delivering orders faster, minimizing errors, and improving customer satisfaction, fulfillment centers directly impact brand reputation, profitability, and scalability.
Atomix Logistics delivers a full spectrum of fulfillment services tailored to ecommerce brands. Whether you need better inventory management, faster ecommerce shipping, or seamless returns processing, Atomix Logistics can transform logistics from a hurdle into a competitive advantage.
Frequently Asked Questions About Fulfillment Centers
What does a fulfillment center do for ecommerce brands?
A fulfillment center manages inventory, picks and packs orders, handles shipping, and processes returns for ecommerce brands, helping them deliver fast and accurate service to customers.
How is a fulfillment center different from a warehouse?
A fulfillment center focuses on fast inventory turnover and shipping integration, while a warehouse is mainly designed for long-term storage with limited operational support.
What are the benefits of outsourcing order fulfillment to a 3PL?
Outsourcing order fulfillment to a 3PL fulfillment center like Atomix Logistics saves costs, improves shipping speeds, increases efficiency, and allows brands to scale without heavy infrastructure investment.
How does inventory management work in a fulfillment center?
Inventory is tracked in real time using advanced software, providing brands with up-to-the-minute visibility, stock alerts, and automated reorder capabilities to prevent stockouts or overstocking.
Why should brands choose Atomix Logistics for fulfillment services?
Atomix Logistics provides reliable fulfillment center solutions with real-time tracking, scalable technology, responsive support, and proven expertise to help ecommerce brands grow faster and serve customers better.
Talk with a team member and get $1,000 of order fulfillment credit*
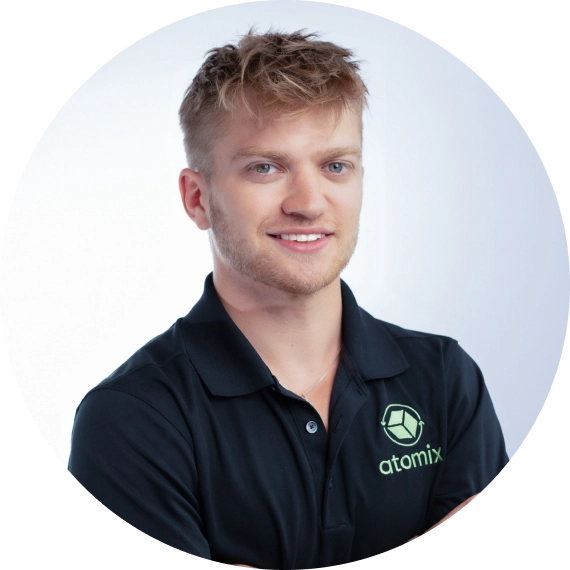
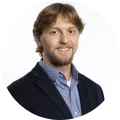
*$1,000 of credit is applied to customers account after Atomix fulfills their 500th order